Plastic, a technical solution
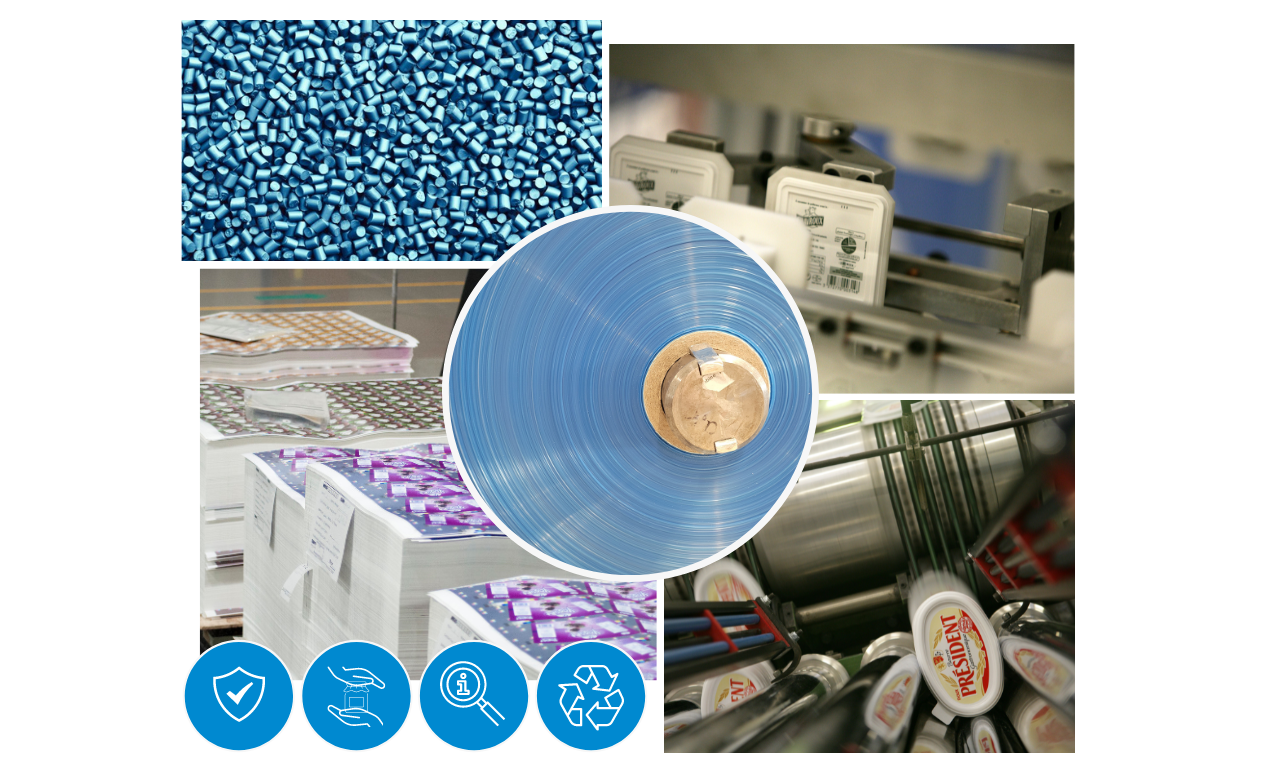
Practical and creative packaging
We control the entire production process for your plastic food packaging, from the design to the manufacturing of the moulds, the printing of the in-mould labels (IML) to the injection moulding or thermoforming of the plastic containers.
This guarantees our customers customization, flexibility and adaptability of lead times.
Monomaterial packaging
Your packaging needs are changing! For 40 years, we’ve been developing single-material plastic packaging to preserve your food products. Thanks to this experience, we can advise you and guide you towards the most appropriate solution. To meet all your technical constraints and commercial objectives, our design office is involved from the outset. Its mission is to develop appropriate packaging while optimising the use of materials. We use the latest injection moulding machines, robots and moulds, enabling us to master the following production techniques.
Injection
This technique allows the manufacturing of complex shapes, sealable or tamper-evident containers, optimised in terms of logistics and wall thickness. Thanks to our technical expertise, we are able to make two-colour parts, items with recloseable dispenser flaps, hinged lids or lids with compartments for a spoon or fork.
Our main decoration process is in-mold labeling (IML). This involves injection-molding a plastic label onto the container. Printing the label flat, like cardboard or paper, ensures high-definition print quality, as well as being 100% recyclable.
Co-injection moulding, a new technology to protect your foodstuffs
This new technology allows us to offer packaging products with an oxygen barriers or light blocking by adding EVOH polymer or a black core whilst offering the same advantages as injection moulding, in particular decoration with IMLs.
Thermoforming
Several families of plastic are used:
- PP
- PET
- PS
To optimise shelf life, tubs can be multilayer with the addition of an oxygen barrier (EVOH) or light blocker. Our thermoformed food packaging is customisable with stickers or by dry offset printing. We can adapt to specific food industry requirements (for all the food trades and even fast food outlets).
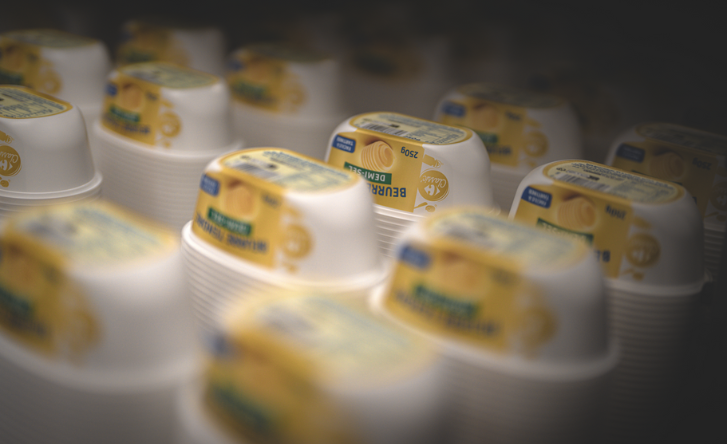
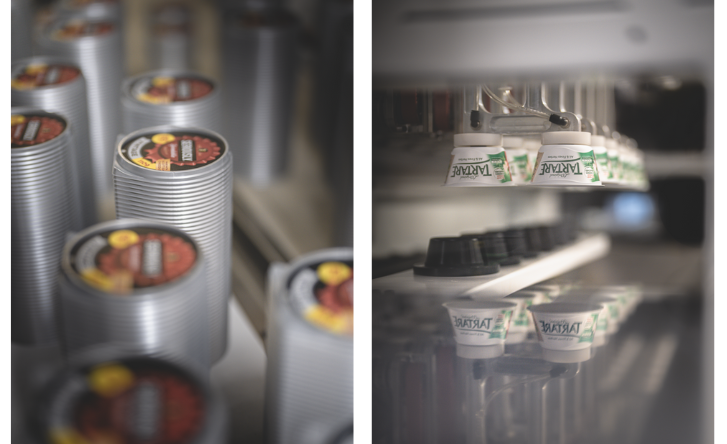
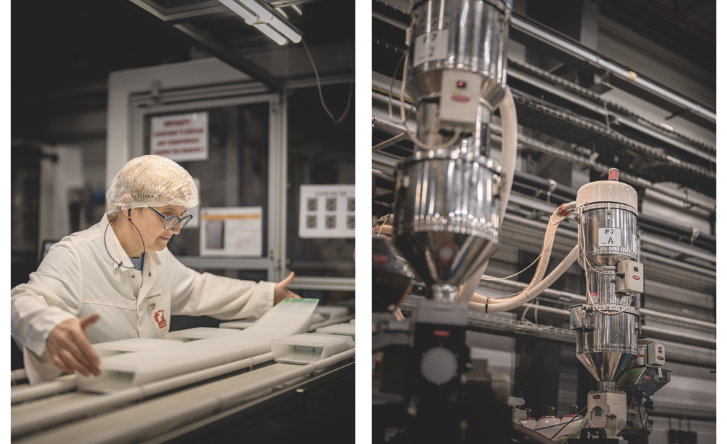
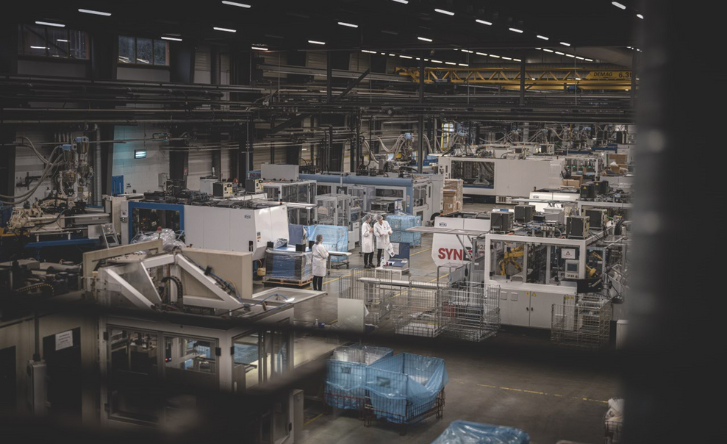
We have a large range of standard packaging products, which can be customised by decoration, and we regularly work on custom packaging solutions for our customers.
The right container for each foodstuff
Using the most suitable resins, our plastic food packaging solutions can be used to pack a wide variety of foodstuffs such as:
- Ice cream
- Dairy products
- Meat products
- Salads,…
Our plastic trays are resistant to freezing, deep freezing, microwave reheating, hot filling, sterilisation and pasteurisation.
Ideal functions for food industry professionals
We offer high-quality food-contact packaging for the agri-food industry. Our wide packaging range means we are able to meet the expectations of consumers as well as food packaging requirements.
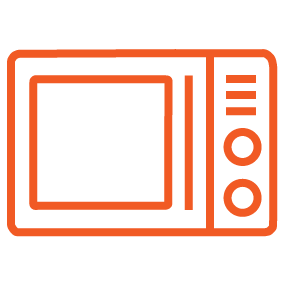
Microwavable or not
Our packaging meets the many needs of your products. From hot filling, to sterilisation and pasteurisation, to freezing and deep-freezing, our teams are here to advise you.
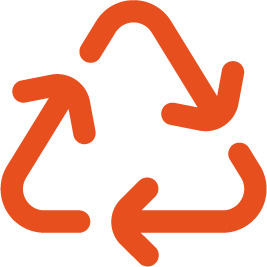
100% recyclable
Our injected plastic food packaging are monoaterial (labels and containers). They are therefore easily recyclable through existing sorting systems. So there’s no loss of material!

Customised packaging
We use IML technique to put labels on our injection-moulded plastic packaging. Printed on our sites, IMLs are infinite source of decoration, the perfect way to give your brand visibility.
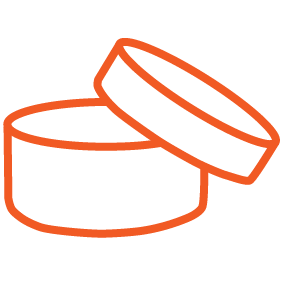
With or without a lid
Our packaging solutions can be sealable or tamper-evident for hermetically sealed products. Maybe you need a recloseable dispenser flap or a hinged lid so the lid does not come off? All you have to do is ask.
A R&D department aware of environmental issues
The Groupe Lacroix started making injection moulded plastic packaging back in 1986.This technique allows for a wide variety of shapes, often complex ones, with endless scope for decoration and, above all, the advantage of being recyclable. A solution in line with our customers’ expectations.
Our design offices in France and North America work with you to develop innovative packaging solutions to meet your needs, using techniques like thin-wall injection moulding and thermoforming.Their constant concern is to reduce the thickness of containers to minimise the environmental impact whilst retaining all their essential technical qualities. All our mono-material (PP, APET) packaging is recyclable and therefore more environmentally friendly.
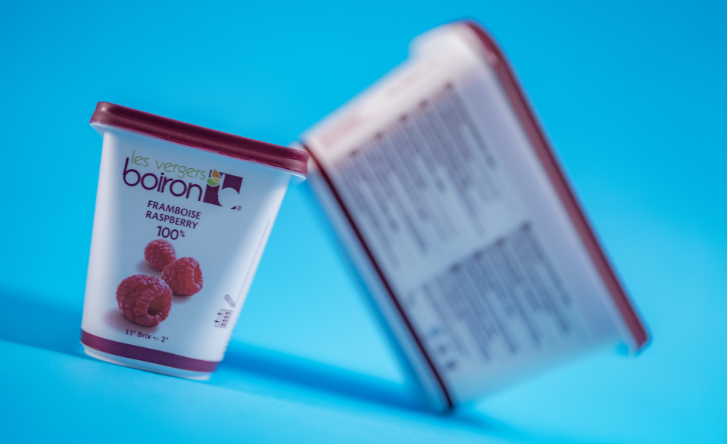
FAQ
What are the advantages of plastic packaging?
Plastic packaging has many advantages. It is lightweight, impact-resistant, relatively cheap and easy to transport. In addition, it is easy to handle and store, making it an economical and practical solution.
What three manufacturing processes are used in our products?
As mentioned above, we use the following three techniques to make our packaging:
How do I know if plastic is food grade?
Plastic is identified with a one-digit code; for food contact opt for 2, 4 and 5 (you will find the number inside a triangle).